The Challenge
The packaging industry is highly competitive, low-margin, and yet capital-intensive. Any investment in new production machinery is therefore subject to stringent performance requirements to make its ROI case.
Bobst, a global leader in machines for the packaging and converting industry, decided to change their approach to machine troubleshooting and customer servicing by integrating ei3’s IoT solutions. Their traditional approach, based on factory technicians and experts dispatched to the customer site, proved to be increasingly expensive in terms of specialist’s time and travel cost. Moreover, the required troubleshooting was not always technical or machine-related: often it linked to a host of factors relating to other processes or personnel in the production cycle.
About BOBST
Founded in Lausanne, Switzerland, Bobst has been making its mark in the packaging world for over 130 years.
- Presence in over 50 countries
- 19 production facilities worldwide
- Over 6100 employees
Read the full case study
The Solution
Based on ei3’s white-labeled remote SERVICE, Bobst launched their ‘Helpline Plus’ service. The adoption of remote SERVICE allowed service technicians to quickly, efficiently, and securely access client machines for trouble shooting without leaving the Bobst office. Secondly, PRODUCTION monitoring provides a full history of process data showing the machine settings and behavior, and operator actions and input, leading up to the machine upset.
In combination, Bobst operators were able to identify, and rectify, machine or process issues with ease and confidence, and were able to present their findings to the client with data to show the root cause of the issue – whether it be the machine or the client’s processes or operators.
Employing various IoT applications helped Bobst improve its overall packaging operations. Bobst’s records show that 80% of all machine-related issues can be found and fixed using ei3 purely remotely, leading to increased customer satisfaction and reduced travel costs – in Bobst estimates, about 2 million USD per year alone. Most important is of course the positive impact this has had on the clients: Thanks to Bobsts unique approach on customer service and satisfaction, backed by ei3, Bobst’s connected machines around the world to date have delivered 340 thousand hours of incident-free service – and counting!
With the bulk of the service conducted online, field service is now able to focus on customer visits where they matter. Backed by 8000 hours of training delivered via ei3, and with ei3’s insights on machine performance and process issues as they arise, the Bobst field service is stronger than ever, standing at 200 service technicians in 52 countries ready to serve customers 24 hours a day.
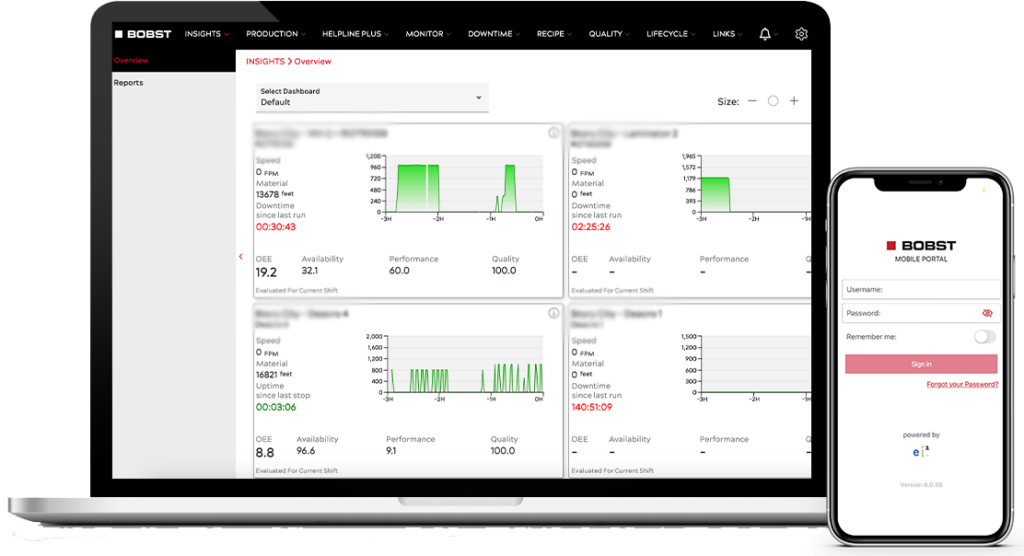
Results
80%
of machine-related issues solved online using remote service
$2 million US dollars
saved in travel costs per year with Helpline Plus
75,000+ Hrs
of troubleshooting delivered with remote access
"At Bobst, we look at connectivity, digitization, automation, and sustainability as the cornerstones of packaging production. We set out on this journey with ei3 in 2004. It has been a close relationship, and we now have over 5000 machines connected."
“If we consider the whole picture, now we can start to measure OEE. We can begin measuring all the different KPIs we're looking for, demonstrating where you're doing well, where you need improvements, and where the value is. And at the end of the day, what this is really giving back is time. All of the above adds up to, for us, our industry vision: a connected factory, and we use ei3, Helpine and Apps to do it.”
“This is a journey which Bobst has been undertaking for the last 15 years with a strategic partner, ei3…and its been a very very close relationship. We have over a thousand installations running in North America, so this is just not a vision, but it is actually happening right now. ”