Last week at the Flower AI Summit 2024 in London, Severin Pang of ei3’s Data Science team unveiled a novel approach to predictive maintenance that has garnered high praise from both industrial leaders and academic circles worldwide. In an era where the line between digital advancement and privacy concerns increasingly blurs, ei3’s approach based on “Inverse-PID” analysis (part of ei3’s ConnectedAI toolbox) stands out for bridging the gap with an innovative solution.
Predictive maintenance, a method aimed at predicting and preventing machine failures before they occur, has long been a focal point for the machinery industry. The traditional reliance on empirical data analysis and engineering-based models, while effective to some extent, often falls short due to data scarcity, model opacity, and a lack of privacy preservation. ei3’s groundbreaking approach takes predictive maintenance to an entirely new height:
Pang’s presentation introduced a robust mathematical framework that analyzes machine behavior beyond mere components, offering a predictive analysis grounded in mathematics rather than just empirical evidence. This method not only enhances the accuracy of maintenance forecasts and is rooted in a traceable mathematical framework that ensures results are self-evident, but also upholds the utmost privacy standards as the method is eminently suited for Federated Learning. This allows decentralized processing of data, ensuring that sensitive information remains within the confines of its origin.
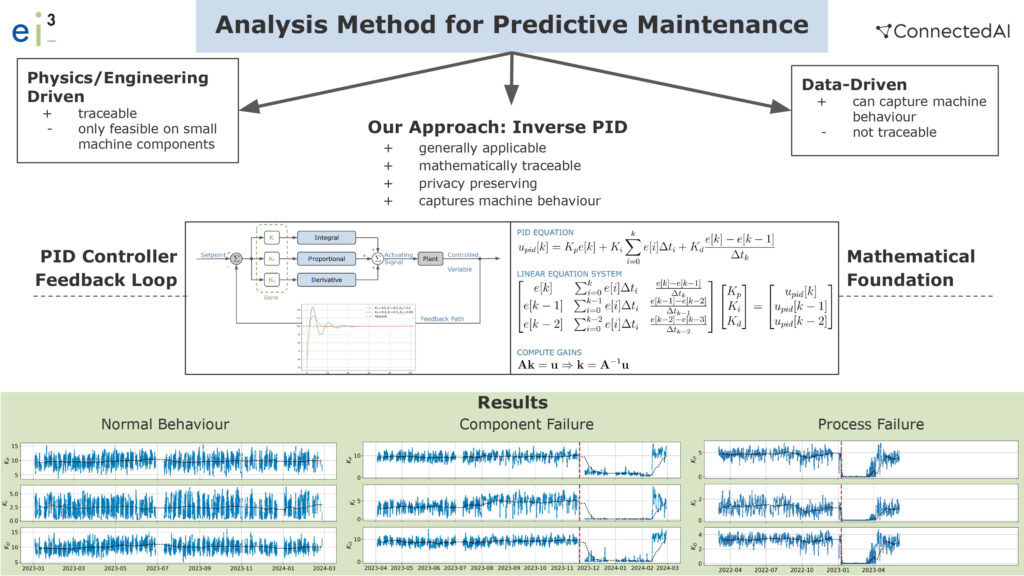
The economic ramifications of unplanned downtime in industrial manufacturing are vast, making effective predictive maintenance strategies more crucial than ever. ei3’s method stands out by addressing these economic concerns through a technology that is generically applicable to a large segment of industrial machines and therefore economically scalable, but also navigating the complex waters of data privacy and model transparency.
Last but not least, machines that run efficiently by avoiding downtime also run more sustainably, an aspect that is of growing concern as manufacturers begin to track the use of energy and resources and the CO2 footprint per manufactured product.
The implications of ei3’s approach extend far beyond industrial machinery. Representatives from the University of Cambridge lauded the method as a “clean approach” with potential applications wherever the stability of self-controlled processes must be monitored, e.g. in self-driving cars, marking a significant milestone in predictive maintenance research.
As the world grapples with the challenges of maintaining high-performance machinery while safeguarding data privacy, ei3’s pioneering data science approach offers a beacon of hope. The acclaim received at the Flower Summit 2024 underscores the industry’s readiness for a shift towards more secure, transparent, and effective predictive maintenance strategies. With ei3 leading the charge, the future of industrial maintenance looks not only brighter but smarter as well.