The Occupational Safety and Health Administration (OSHA) is a familiar standard in the manufacturing environment. Industrial equipment builders and owners alike prioritize employee safety at the highest level, and in turn OSHA requires that each employer offer a work environment that is free of hazards.
The OSHA general duty clause, Section 5(a)(1) of the Occupational Safety and Health Act, requires that each employer furnishes to each of its employees a workplace that is free from recognized hazards that are causing or likely to cause death or serious physical harm.
Manufacturing in the new era of Covid-19 requires new hazards to be broadly recognized and safety and procedural standards for employers updated accordingly to protect employees. The new procedures may require – taking of temperatures, limitations on central meeting areas such as cafeterias and break rooms, and the use of personal protective equipment for those that encounter the general public.
Conversely most factory settings are considered by OSHA to be low to moderate risk for Covid-19 exposure, and replicate little of the high-risk environment of what is being seen in the inpatient medical world. Low or moderate risk does not mean no risk, and employers who take proper precautions can further mitigate risk for their employees.
The CDC, though, has been open in their determination of what constitutes close contact and the frequency of close contact overall, which leaves states, municipalities, and ultimately the courts the right to interpret those guidelines. Many states are forming restrictive details, which includes close contact as anything inside six feet, and the frequency of that contact as short as 10 minutes of exposure. The ability to operate, service or repair equipment inside protocols while keeping distance and maintaining that time interval creates a challenge for industrial machine manufacturers and equipment owners.
As an additional safeguard measure for their employees, should equipment owners require a policy stance on how a machine builder’s service team can securely and remotely connect to a piece of industrial equipment?
Industrial equipment is the lifeblood of manufacturing, and employees have always been empowered to call out safety issues, and equipment builders have worked long and hard to make their equipment safe to operate. In today’s environment, it is crucial to structure the safety protocols, policies, and procedures around the serviceability of those machines, essential employee access to those machines, and general safety needs.
Servicing equipment is critical both to restarting furloughed machines, and machines that are seeing increased usage due to customer demand. Allowing an equipment technician into your plant in today’s environment will come with additional questions not asked three months ago. With that in mind, the secure service that ei3 provides to our manufacturing customers allows OEMs to securely establish connectivity to the equipment, based on the equipment owner’s approval, and let the OEM service provider perform the necessary diagnostic work in a remote environment. This activity reduces potential exposure for both the machine owner’s team and the OEM service provider.
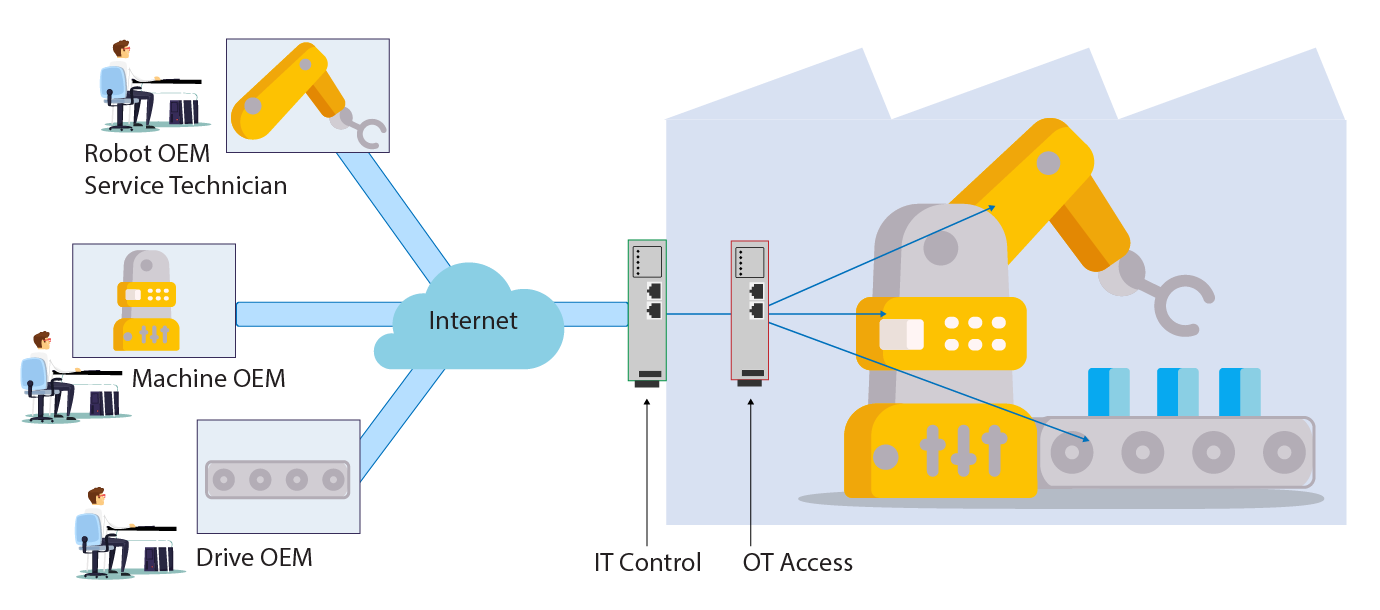
The above image illustrates ei3’s two-tier edge device architecture, providing granular access for remote troubleshooting and management of machines, ensuring secure remote access to machines.
The connection of ei3’s remote service is tried and true with twenty years of experience and the knowledge of thousands of installations in more than 100 countries – The minimal service expense can be blended through the plant processing, maintenance, and safety budget.
Additionally, while we recover from the widespread fear of Covid-19, many employees will find that they are not comfortable coming back to work, where an outbreak took place or where there were pockets of exposed personnel, regardless of whether or not this happened on the job. Employers should expect to perform reasonable accommodations for these employees, by allowing them to telework or creating workarounds to avoid contact with fellow employees as much as possible.
For essential employees, with these lingering fears, the ei3 solution again provides a way to be in touch with tangible data, securely delivered both inside and outside of the plant environment. The same metrics available on HMI screens are deliverable virtually to employees that desire a lower involvement with their co-workers.
General safety needs cover the good faith effort of the employer to comply with the suggestions and guidelines of the Center of Disease Control (CDC), OSHA, and ADA. In many cases courts view the documented good faith accommodation efforts of employers as key evidence in a situation where an employee was harmed or sickened. OSHA has proactively published several guidelines in March of 2020 outlining the workplace guidance relating to what employers should produce for their teams. Among those considerations was a process to Develop, Implement, and Communicate about Workplace Flexibilities and Protections.
While many employers will be offering suggestions on taking temperatures, advanced cleaning solutions, and the like, a number of employers will find additional benefit in informing employees that they were able to continue operations through virtual measures such as ei3 remote connectivity to key pieces of industrial equipment. Further improving the good faith efforts by allowing those connected equipment providers to service those machines securely and remotely and providing access as a reasonable accommodation to those employees who request it.
The environment that we operate in is extremely fluid, and none of us can predict the future, the final impact from this solution or the continuing work environment. At ei3, we have a proven solution with a minimal expense structure, which offers an additional layer of protection, accommodation, and secure communication for our OEM partners and their customers, who today more than ever, are searching for ways to reopen their businesses safely, while accommodating the varied needs of their essential employees.
To learn more about ei3’s remote access solution, download our whitepaper on “The New Remote Access.” Whether you have a solution, think you need one, or worry about the next audit from your corporate compliance team receive our bonus checklist to verify your approach. Take action to be ready and compliant.